Kurze
Geschichte der Zinkhütte Harlingerode
Im
Rahmen der Aufrüstung und Autarkiebestrebungen der Nationalsozialisten
sollte die Metallproduktion der Unterharzer Berg- und Hüttenwerke bei
Goslar stark gesteigert werden. Unter der Bezeichnung
"Rammelsbergprojekt" begann 1935 der Aus- und Neubau der
Bergwerks- und Hüttenanlagen. Im Rahmen des Rammelsbergprojekts entstanden
so ab 1935 die neue Aufbereitung (Flotation) am Erzbergwerk Rammelsberg in
Goslar und die Zinkhütte Harlingerode. Für beide Neubauvorhaben konnte die
Architektengemeinschaft Fritz Schupp und Martin Kremmer gewonnen werden, die schon in Essen mit der Zeche Zollverein XII
(1929-32) bedeutende Industriebauten geschaffen hatten.
Als
Standort der zukünftigen Zinkhütte wählten die Unterharzer Berg- und
Hüttenwerke ein bisher ungenutztes Gelände in der Nähe der
Blei-Kupfer-Hütte Oker (heute Goslar-Oker) und der Zinkoxidhütte Oker. Da
dieses Gelände in der Gemarkung Harlingerode (heute Bad
Harzburg-Harlingerode) lag, erhielt die Hütte den Namen Zinkhütte
Harlingerode. Hier begann 1935 der Bau der Betriebsgebäude nach den Plänen
von Schupp und Kremmer als Stahlfachwerkbauten. Bei dem Entwurf waren
luftschutztechnische Belange zu berücksichtigen. So entstanden die beiden
Ofenhäuser Ost und West spiegelbildlich symmetrisch rechts und links einer
Mittelachse. Viele Anlagenteile waren doppelt vorhanden, so daß auch bei
Zerstörung eines Anlagenteils der andere weiterarbeiten konnte.
Grundlage
der zukünftigen Zinkhütte war ein Zinkkonzentrat mit einem Zinkgehalt von
ca. 43%, daß erst dank der neuen Aufbereitung aus den stark verwachsenen
Erzen des Erzbergwerks Rammelsberg gewonnen werden konnte. Verschiedene
Vorversuche führten zu der Entscheidung, zur Zinkgewinnung das
New-Jersey-Verfahren zu verwenden, das in den USA und England schon mit
Erfolg genutzt wurde.
Schon
im Dezember 1936 konnte versuchsweise die Zinkproduktion mit vorerst 5
Retorten aufgenommen werden, der die offizielle Inbetriebnahme im Januar 1937
folgte, obwohl
die Bauarbeiten noch weiterliefen. Erst 1938 wurde das Ofenhaus Ost
und die Feinzinkanlage vollständig fertiggestellt. Bis 1940 konnten dann alle geplanten Anlagen in Betrieb genommen
werden, so daß seit diesem Zeitpunkt auch zusätzlich Erzkonzentrate aus dem Oberharzer
Bergwerk Bad Grund sowie den Aufbereitungsanlagen in Clausthal und
Lautenthal verarbeitet wurde.
Trotz anfänglicher Probleme mit der Stabilität der Retorten,
kriegsbedingten Versorgungsproblemen und häufigem Fliegeralarm, konnte
die Zinkproduktion in den folgenden Jahren kontinuierlich gesteigert werden.
Als Ersatz für zum Militärdienst eingezogene Belegschaftsmitglieder wurden
ab 1943 auch Zwangsarbeiter in der Hütte beschäftigt. Für sie entstand ein
Barackenlager südlich der Straße von Oker nach Harlingerode, von dem noch
heute Fundamente zeugen.
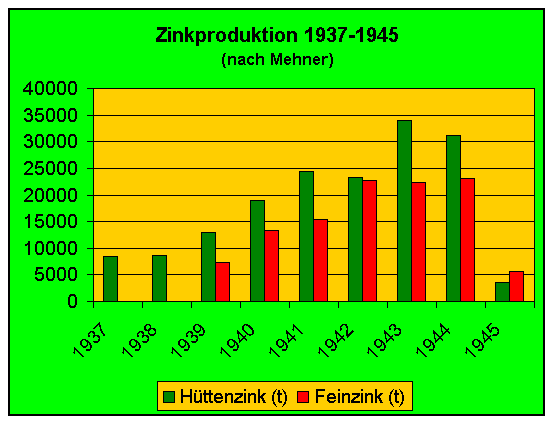
Im
April 1945 kam die Zinkproduktion nach Besetzung durch Amerikanische Truppen
vollständig zum Erliegen. Erst im Dezember 1945 konnte die Produktion -
wenn auch vermindert - wieder aufgenommen werden. Bis 1953 stieg sie dann
auf einen Wert von annähernd 50.000 t Hüttenzink. In diesen Jahren nahm
man auch noch eine Reihe von Verbesserungen und Modernisierungen an den Anlagen
vor. Diese Arbeiten konnten 1953 abgeschlossen werden.
Zu
Beginn der 1960er Jahre kam es dann erstmals zu Preiseinbrüchen bei Zink
und in Folge zu einer Reduzierung der Belegschaft.
Im
Jahr 1967 wurden dann die Unterharzer Berg- und Hüttenwerke von der
PREUSSAG AG erworben, die zwischen 1968 und 1970 die Anlagen erheblich
erweitern ließ. Hierbei verlängerte man beide Ofenhäuser, um weitere 10
Retorten aufnehmen zu können. Durch organisatorischen Zusammenschluß der
Bleihütte Oker, der Zinkoxydhütte und der Zinkhütte Harlingerode entstand
1968 das Hüttenwerk Harz.
Im
Oktober 1972 erfolgte die Einstellung der Feinzinkproduktion, da
elektrolytisch erzeugtes Feinzink, daß deutlich billiger produziert werden
konnte, auf den Markt drängte. Bis zum Ende der 1970er Jahre stieg dann die
Produktion von Hüttenzink auf 99.000 t im Jahr an.
Aufgrund
gestiegener Energiekosten und hoher Umweltauflagen erfolgte Ende 1981 die
Stillegung des Röstbetriebes mit der angeschlossenen Schwefelsäureherstellung. Das
Rammelsberger Zinkkonzentrat konnte jetzt nicht mehr verarbeitet werden und
wurde bis zur Stillegung des Erzbergwerks 1988 an andere Hütten verkauft.
Infolge dieser Betriebseinschränkungen legte man in Dezember 1981 das
Ofenhaus Ost still, daß später zu einer Lagerhalle umgebaut
wurde. Zur Verarbeitung kamen jetzt nur noch oxidische Erze und
Vorstoffe. Diese stammten zu einem großen Teil aus dem Ausland.
Die
gegen Ende der 1980er Jahre stark gefallenen Zinkpreise ließen den
Weiterbetrieb der Hütte nicht mehr wirtschaftlich erscheinen, so daß die
Firma Harz-Metall GmbH die Zinkproduktion offiziell am 30. Juni 1988
einstellte.
Als
Nachfolgebetrieb übernahm die neugegründete Harzer Zink GmbH die Hütte im Jahr
1989 und führte die Produktion von Zinkoxid und Zinkstaub weiter. Dazu
erfolgte die Produktion von Zink als Vorstoff in einer sogenannten
Minihütte mit maximal 10 Retorten. Dieser letzte Hüttenbetrieb wurde dann
im Juni 2000 entgültig eingestellt. Seit diesem Zeitpunkt erfolgt in den
Gebäuden der Zinkhütte Harlingerode nur noch die Produktion von Zinkoxid
und Zinkstaub als Vorstoff für andere zinkverarbeitende Betriebe.
Nachdem
schon in den 1990er Jahren etliche nicht mehr genutzte Gebäude der Hütte
abgerissen wurden, folgt im Herbst 2003 das ehemaligen Ofenhaus Ost.
Der
Autor möchte sich herzlich bei dem Betriebsdirektor Herrn Dr. Ulrich Kerney
bedanken, der es ihm im Oktober 2003 ermöglichte, eine Reihe von Aufnahmen
der verbliebenen Gebäude zu machen.
Zink
"HARZ" - Zinkgewinnung auf der Zinkhütte Harlingerode
Der
im Folgenden wiedergegebene Text ist der gleichnamigen Broschüre der
Unterharzer Berg- und Hüttenwerke aus dem Jahr 1956 entnommen:
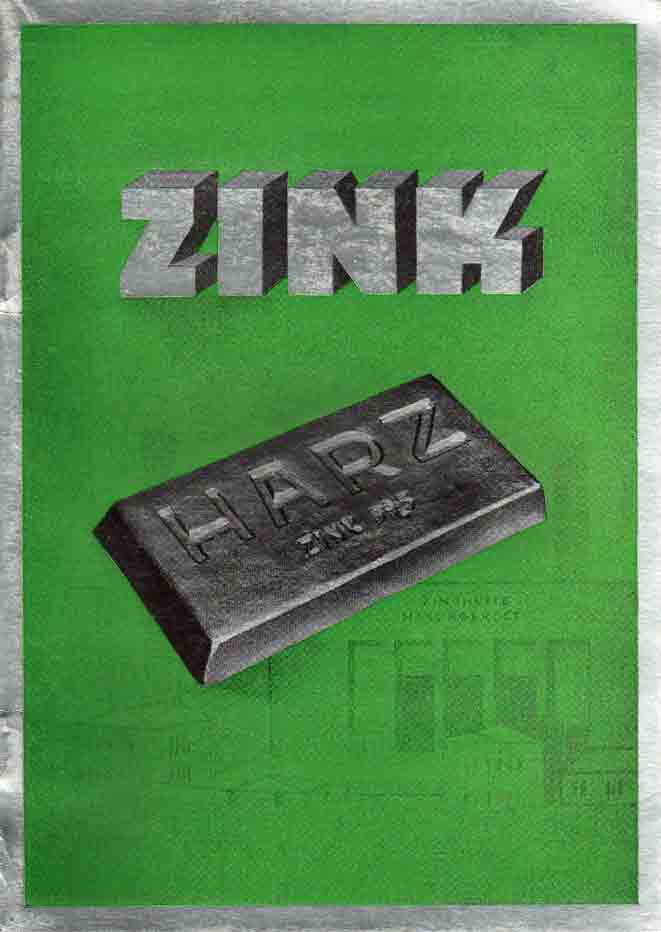 |
Titel
der Broschüre Zink "HARZ" Goslar
1956 Original Sammlung:
Joachim Fricke
|
Vorwort
Zink "Harz" - unter diesem Titel überreichen wir
allen Interessenten und Verbrauchern die vorliegende Schilderung der
Zinkgewinnung auf der ZINKHÜTTE HARLINGERODE.
Die kurzgefaßten Ausführungen sollen die oft gestellten
Fragen nach Herkunft und Gewinnungsverfahren der einzelnen Zinksorten, die unter
dem Namen "HARZ" bekannt sind, beantworten.
Unterharzer Berg- und Hüttenwerke
GmbH.
Zinkhütte Harlingerode
Eine ganz kurze Geschichte des Zinks
Verhältnismäßig spät ist das Zink als elementares Metall
erkannt worden, und unentwegt mühten sich die mittelalterlichen Alchimisten mit
einem sonderbaren Erz ab, welches gemeinsam mit Kupfer oder kupferhaltigen Erzen
geschmolzen anscheinend Gold ergab. Aber es war kein Gold, trotz der schönen,
glänzend gelben Farbe. Das alchimistische Ergebnis, das, was die Alchimisten -
unter Anwendung geheimnisvoller Zeremonien und im Banne mystischen Aberglaubens
befangen - in mühseliger Arbeit entdeckten, war nicht der "Stein der
Weisen", es war nicht jener Stein, der alle Metalle in Gold verwandeln
sollte, sondern es war - Messing!
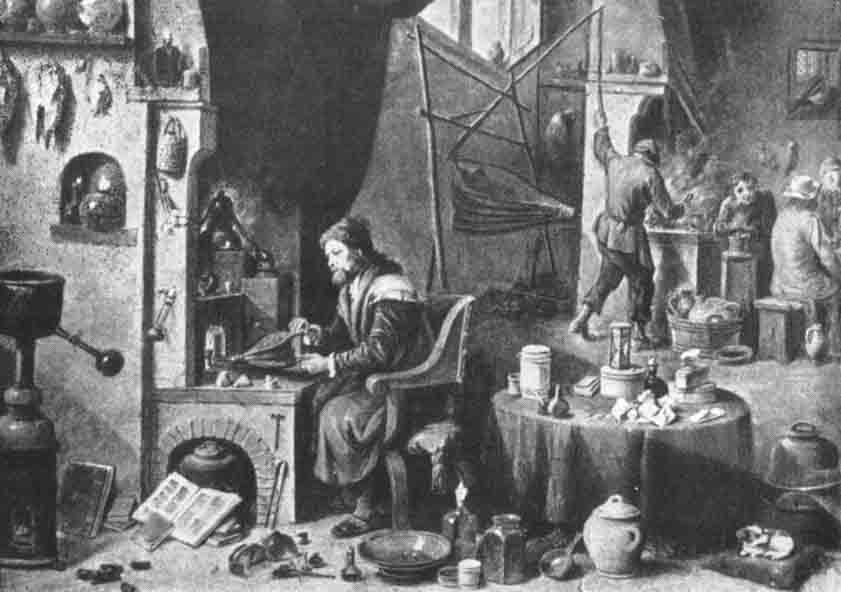
Der Alchimist
Erbost und verbittert darüber, daß das glänzende Metall
unter ihren Händen sich alsbald verfärbte, grau, braun und schwarz wurde und
in scharfen Säuren sich brausend löste, während das echte Gold bei gleicher
Behandlung sich kaum veränderte, belegten die Enttäuschten das ihnen
unbekannte Metall mit den verächtlichsten Namen: Halbmetall, Bastard und
Zwitter.
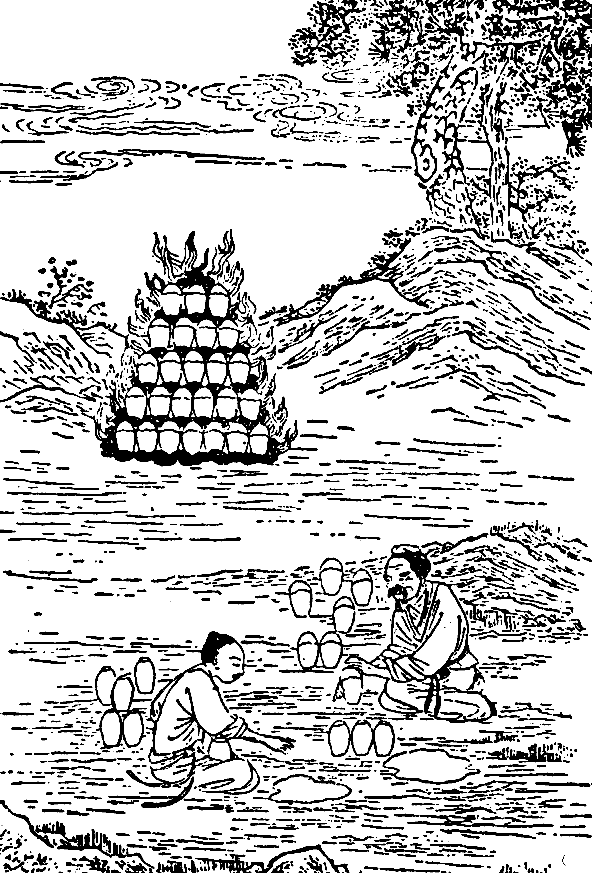
Zink-Verhüttung in China (etwa
16. Jahrh.)
Es gelang also den Alchimisten nicht, das metallische Zink
seinem Erz zu entreißen. Nur durch die Herstellung von Messing aus Kupfer und
kupferhaltigen Erzen, gemeinsam mit dem kerbig-zackigen, dem
"zinkigen" Erz, war das Zink als bastardhafter Partner bekannt. Selbst
ein so hervorragender Bergmann wie Georg Agricola, der von 1495 bis 1555 lebte,
erkannte nicht den metallischen Charakter des Zinks, obwohl er den Namen
"Zink" in seinen Büchern verwendet. Selbst dann, als metallisches
Zink aus China und Indien gegen Ende des 16. Jahrhunderts in Europa auftauchte,
benannte man es immer noch nach seinem bekanntesten Erz, dem Galmei (calaem),
oder nach seinem damaligen Herkunftsland "Indisches oder Malabar-Blei oder
-Zinn".
Erst Löhneiß (1617) sprach das Zink als elementares Metall
an und nannte es bei dem Namen, den es heute noch führt.
Aber weitere hundert Jahre sollten vergehen, ehe in Europa
metallisches Zink nach streng geheimgehaltenen Regeln hergestellt wurde. Im
Jahre 1746 endlich gab der Chemiker Marggraf sein Verfahren zur Verhüttung des
klassischen Zinkerzes, des Galmei, durch Reduktion mit Kohle unter Luftabschluß
bekannt.
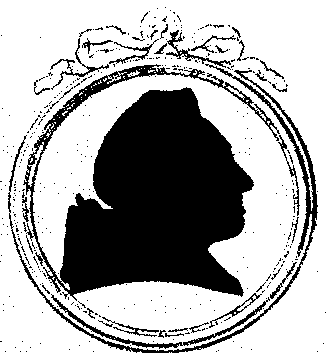
Andreas Sigismund Marggraf
(1709 - 1782)
Die Richtung zur Gewinnung von Zink war damit gewiesen, jedoch der Weg noch nicht
genau vorgezeichnet. Erst der durch den Hüttenmeister Ruberg (1800) in Ober-Schlesien entwickelte "liegende Muffel"-Prozeß gab die
Möglichkeit, Zink industriell zu erzeugen.
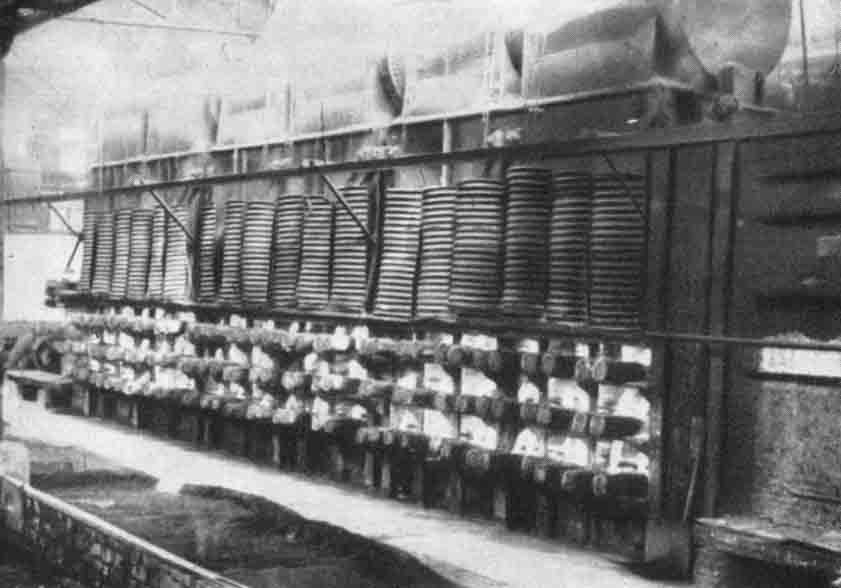
Zinkofen mit "liegenden
Muffeln"
Nun ging die weitere Entwicklung rasch voran. England stellte
zwar schon 1730 in ganz kleinen Mengen Zink her, doch erst der "liegende
Muffel"-Prozeß gestattete die wirtschaftliche Gewinnung von Zink im
Großen. Nach diesem Verfahren, welches mit der Zeit eine ganze Anzahl von
Verbesserungen erfuhr, wird noch heute Zink gewonnen. Allerdings nicht mehr aus
dem klassischen Galmei allein - dieses Erz ist in Europa schon fast restlos
ausgebeutet - sondern aus den sulfidischen Erzen, in welchen das Zink an
Schwefel gebunden ist.
Mit der Nutzbarmachung der Elektrizität für die Industrie
kommen nun elektrothermische und elektrochemische Gewinnungsverfahren auf, die
jedoch an einen sehr billigen Strom gebunden sind.
Eine recht weitgehende und neuzeitliche Abwandlung des
"liegenden Muffelverfahrens" stellt die Gewinnung des Zinks in der
"stehenden" - oder "Vertikal-Retorte" dar. Hierauf wird
weiter unten bei der Beschreibung der Zinkverhüttung im Harz noch näher
eingegangen.
Das älteste Hauptanwendungsgebiet für das Zink liegt in der
Messingherstellung, wie diese bereits von den Assyrern und Babyloniern ausgeübt
wurde, indem sie Kupfer mit "Erde" schmolzen. Viel später, im Jahre
1812, wurde das Walzen von Zink eingeführt, dem 1836 das Verzinken von eisernen
Gegenständen folgte, während die Zinkfarben-Herstellung in industriellem
Ausmaß im Jahre 1844 aufgenommen wurde.
Eine verhältnismäßig neuere Verwendung fand das Zink
während der Jahre des ersten Weltkrieges, zu welcher Zeit Zinklegierungen
hergestellt wurden. Diese Zinklegierungen, für welche handelsübliches
Hüttenzink verwendet wurde, bewährten sich jedoch nicht, weil die schädigende
Wirkung der im Hüttenzink vorhandenen Begleitmetalle damals nicht bekannt war.
Erst die Möglichkeit, ein sehr reines Zink mit nur ganz geringen
Verunreinigungen, das Feinzink, herzustellen, eröffnete der
Feinzinklegierungs-Herstellung neue und aussichtsreiche Wege. Es war ein langer
und mühseliger Weg, der zum Zink führte, und es besteht ein großer
Unterschied zwischen dem Schmelzen von Kupfer und "Erde" und der
jetzigen modernen Verhüttung von Zinkerzen.
Wenn man heute durch eine moderne Zinkhütte geht und den
maschinellen und apparativen Aufwand mit seinen Zerkleinerungsmaschinen,
Förderbändern, Kränen, Gasgeneratoren, Sinterbändern, Mahl- und Mischmaschinen, Pressen, Verkokern,
Reduktions-Retorten, Kondensatoren und Meßwarten in sich aufnimmt, dann kann man
ermessen, welchen Schwierigkeiten die Alchimisten gegenüberstanden, als sie den
"Stein der Weisen" suchten und nur einen Bastard fanden.
Es ist vielleicht angebracht,
an dieser Stelle daran zu
erinnern, daß es auch heute nicht ganz so einfach ist, ein gutes Hüttenzink zu
erzeugen, und daß es viel Mühe und Arbeit, Energie und Wissen erfordert, ehe
das blausilbern schimmernde Metall in stetem Fluß die Formen füllt.
Den "Stein der Weisen" zu finden wird auch der
Neuen Zeit nicht gelingen, wohl aber gelang ihr die Herstellung des metallischen
Zinks. Der Bastard der Alchimisten lebt nur noch in den alten Schriften.
Die Gewinnung von Zink "HARZ" in der
Vertikal-Retorte
Dieses Verfahren zur Gewinnung von metallischem Zink aus
seinen Erzen, wie es in Amerika von der New Yersey Zinc Co. 1930 entwickelt
wurde, findet auch auf der Zinkhütte Harlingerode Anwendung. Es ist eine der
fortgeschrittensten Verhüttungsmethoden für Zinkerze.
Ehe mit der Beschreibung des Verfahrens begonnen werden soll,
muß noch einiges über die Vorstoffe, insbesondere über die zinkhaltigen Erze
gesagt werden.
Die Vorstoffe
Die Unterharzer Berg- und Hüttenwerke GmbH. betreiben das
Erzbergwerk Rammelsberg bei Goslar, das über eine Lagerstätte mit einem
reichen, jedoch sehr fein verwachsenen Erz verfügt, Seit über tausend Jahren
sind hier im Harz die Bergleute am Werk und schürfen in
der Tiefe von über 400 Metern nach Erz. Der Rammelsberg bei Goslar, der alten
Kaiserstadt, stellt eine geologische Besonderheit dar. Vor Jahrmillionen, als
der Harz noch vulkanisches Gebiet war, entstand hier eine große erzführende
linsenförmige Lagerstätte, deren Entstehung nach neuesten Erkenntnissen auf
untermeerische (submarine) vulkanische Ausbrüche mit den damit verbundenen
Ablagerungen zurückzuführen ist.
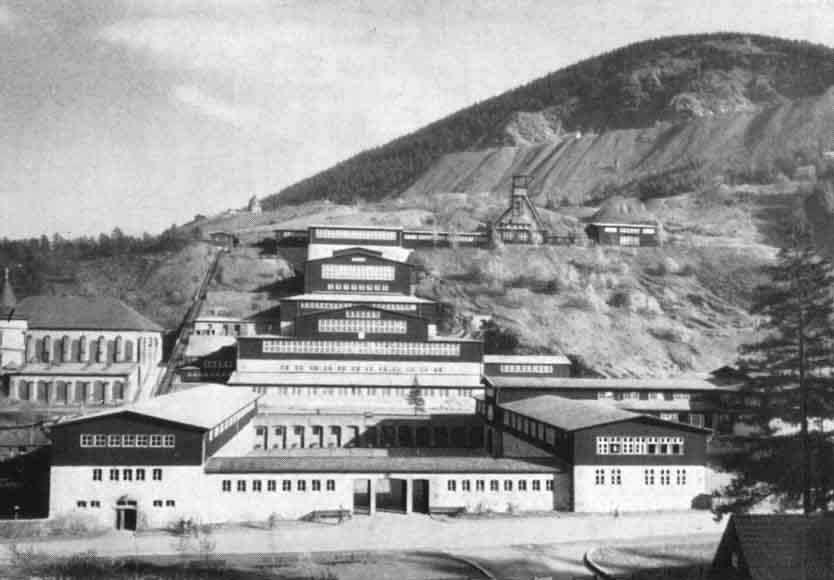
Das Erzbergwerk Rammelsberg
In modernen Erzaufbereitungsanlagen wird das im Tiefbau
geförderte Roherz aufgeschlossen und in drei Konzentraten angereichert. Bei den
Aufbereitungs-Konzentraten aus dem reichen Lagererz nimmt das Zink-Konzentrat mit
etwa 30 % der Roherzmenge den Hauptanteil ein, während ein kupferhaltiges Blei-Konzentrat und
ein pyritisches Konzentrat je 15 % der Roherzmenge betragen.
Der Rest von etwa 40 % besteht aus zu verhaldenden Abgängen.
Auch die armen Randpartien des Erzlagers werden abgebaut,
aber mit einer geringeren Konzentrat-Ausbeute aufbereitet. Die unhaltigen
Abgänge belaufen sich hier auf über 70 % der Roherzmenge. Die Konzentrate
jedoch haben etwa die gleiche Zusammensetzung wie die aus reichem Lagererz
gewonnenen.
Das für die Zinkgewinnung bestimmte Zink-Konzentrat enthält
43 - 44 % Zink und wird dem Zinkverhüttungs-Prozeß zugeführt.
Der Zinkinhalt des Blei-Konzentrates mit 17 % Zink fällt
zunächst in einem Bleihütten-Prozeß als zinkhaltige Schlacke an, die in
gesonderten Arbeitsgängen auf Zinkoxyd verblasen wird.
Als weiteres Bergwerkserzeugnis steht ein reiches
Zinkkonzentrat mit 59 % Zink aus dem Oberharzer Gangerzbergbau zur Verfügung,
das von der an den Unterharzer Berg- und Hüttenwerken beteiligten
"Preußag" geliefert wird.
Außerdem werden in einem besonderen Werk, das auf der Basis
eigener Halden aus der früheren Verhüttungsperiode des unaufbereiteten
Roherzes arbeitet, weitere Vorstoffe in Form von Zinkoxyd hergestellt.
Alle Zinkoxyde werden in einer Drehrohrofen-Anlage geklinkert
und weitgehend vom Blei befreit. Das anfallende geklinkerte Zinkoxyd enthält
nunmehr 65 bis 70 % Zink.
Die der Zinkhütte Harlingerode zur Verfügung stehenden
Vorstoffe sind demnach:
|
Rammelsberger Zinkkonzentrat |
|
|
Oberharzer Zinkkonzentrat |
|
|
Geklinkertes Zinkoxyd. |
|
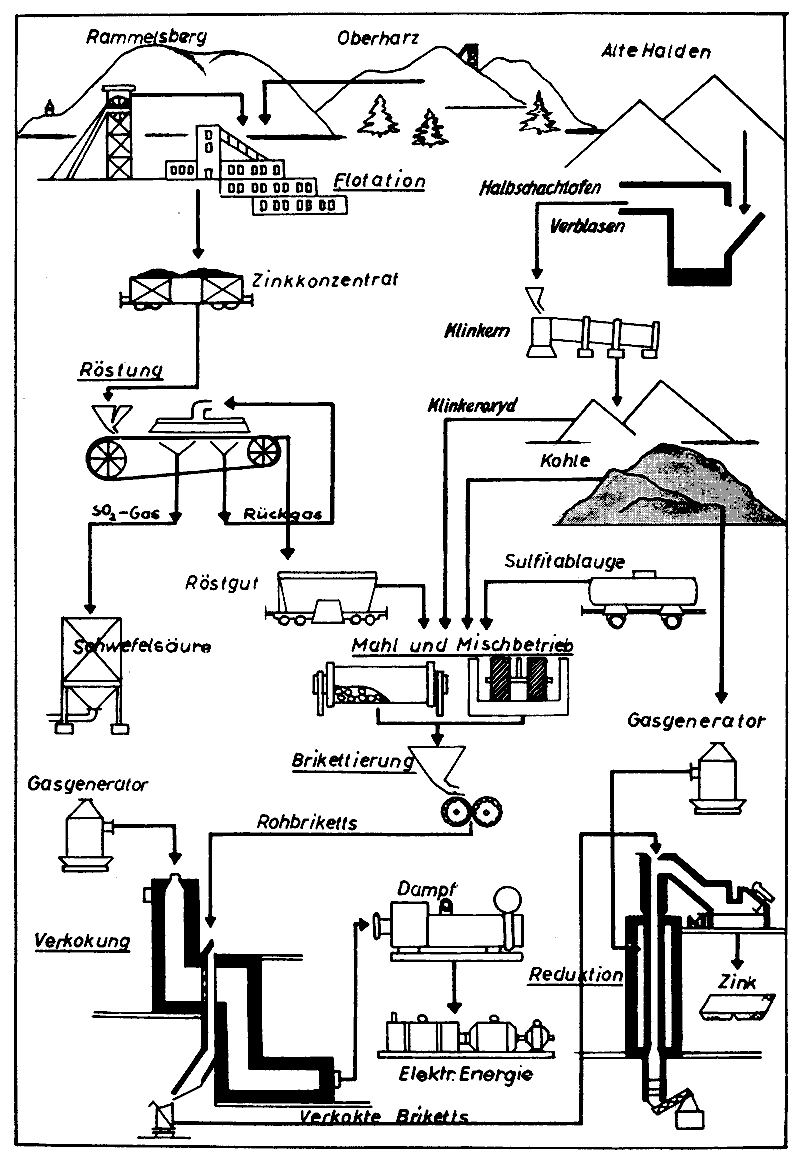
Stammbaum
der Zinkgewinnung nach dem Verfahren der New Jersey Zinc Co. auf der Zinkhütte
Harlingerode
Die Gewinnung von Zink 99,5 "HARZ"
Alle oben genannten Vorstoffe werden auf der
"Zinkhütte Harlingerode" verhüttet, deren Bau 1935 von den
"Unterharzer Berg- und Hüttenwerken" begonnen wurde. Die
Hüttenanlagen liegen etwa auf halbem Wege zwischen Goslar und Bad Harzburg am
Nordrand des Harzes in nächster Nähe der kleinen Stadt Oker in der Gemarkung
Harlingerode.
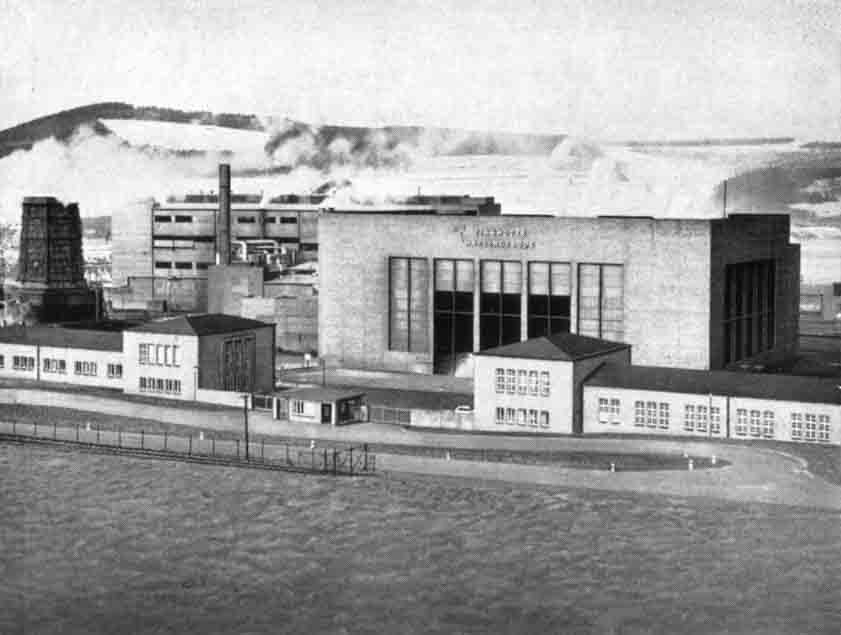
Teilansicht der Zinkhütte
Harlingerode (Mittelteil)
Dies moderne, nach dem Verfahren der
"New Jersey Zinc Co." arbeitende Werk wurde nach dem Kriege auf seine volle
Leistungsfähigkeit ausgebaut und ist heute etwa mit einem Drittel an der
westdeutschen Hüttenproduktion beteiligt.
Die Verhüttung der Zinkkonzentrate geht in mehreren Stufen vor sich:
|
1. Röstung, |
|
|
2. Mischung und Brikettierung, |
|
|
3. Verkokung, |
|
|
4. Reduktion. |
|
Die Röstung
Die Zinkkonzentrate mit einem Schwefelgehalt von 30 % werden
zunächst auf zwei großen Band-Sinterapparaten geröstet, wobei ein sehr
schwefelarmes Röstgut mit 54 bis 58 % Zink entsteht. Die Röstgase enthalten
den aus den Erzen stammenden Schwefel. Sie werden in einer Kontakt-Anlage auf
handelsfertige Schwefelsäure verarbeitet.
Diese Röstung der Zinkkonzentrate bewirkt, daß das an
Schwefel gebundene Zink von ersterem befreit wird. In Verbindung mit Wärme und
dem Sauerstoff der Luft wird der Schwefel verbrannt, d. h. er verbindet sich mit
dem Sauerstoff zu Schwefeldioxydgas welches vom Sinterband dauernd abgesaugt wird. Das vom
Schwefel befreite Zink reißt in gleichem Maße wie der Schwefel entweicht,
ebenfalls Sauerstoff an sich und geht dadurch in Zinkoxyd über.
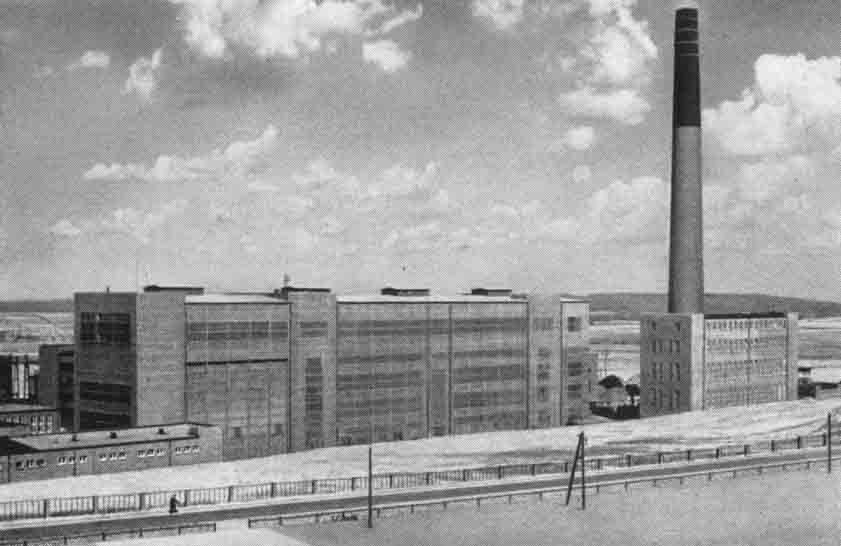
Rösthütte und
Schwefelsäure-Anlage
Faßt man den Röstprozeß in einer vereinfachten chemischen
Formel zusammen, so erhält man:
ZnS + 3 O = ZnO + SO2
Das schwefelhaltige Zinkkonzentrat ist durch die Röstung zum
"Röstgut" geworden und besteht nun zu 67 bis 72 % aus Zinkoxyd.
Dieses Röstgut liegt nun in der zur Verhüttung notwendigen
Form vor und kann mit den geklinkerten Zinkoxyden vereinigt werden.
Die Mischung und Brikettierung
Damit die Zinkträger - das Röstgut und das Klinkeroxyd - so
innig wie möglich mit dem Reduktionsmittel, der Kohle, in Berührung kommen,
müssen sie fein gemahlen und sorgfältig miteinander gemischt werden. Dieses
geschieht durch Zerkleinern des Röstgutes in Stachelwalzen, Symonsbrechern,
Feinmahlen in Kugelmühlen und Mischen in schweren Kollergängen.
Aber noch immer ist diese genau dosierte
Zinkträger-Kohlemischung nicht so weit, daß sie dem eigentlichen
Verhüttungs-Prozeß zugeführt werden kann. Sie muß erst in "Form"
gebracht werden. Dieses geschieht durch die Brikettierung. Während der letzten
Stufe der Durchmischung in den Kollergängen werden dem Gemisch noch Bindemittel
und Sulfitablauge hinzugefügt, die es brikettierfähig machen. In den
Brikettpressen entstehen unter hohem Druck Rohbriketts in Kissenform von etwa
600 Gramm Gewicht.
Ehe diese Rohbriketts in die
Reduktions-Retorten gelangen,
müssen sie jedoch noch eine Vorbehandlung durchmachen, die man Verkokung nennt.
Die Verkokung
Die Verkoker bestehen aus Gitterschächten, in welchen die
Rohbriketts auf etwa 800°C erhitzt werden. Sie verlassen die Verkoker durch
eine Austrags-Vorrichtung in glühendem Zustand.
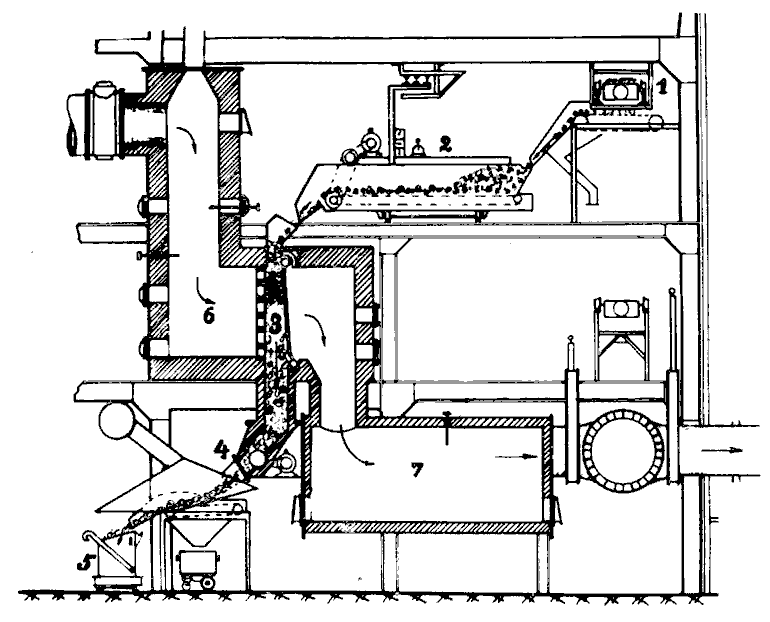
Schematischer
Schnitt durch einen Verkoker
1
Becherwerk, 2 Beschickungswagen, 3 Gitterschacht,
4
Austrag, 5 Beschickungskübel, 6 Brennkammer, 7 Staubkammer
Während des Verkokungs-Prozesses entweichen die flüchtigen
(bituminösen) Bestandteile der Kohle und die Feuchtigkeit. Das vorher kompakte
Brikett wird durch Koksbildung porös und fest. Die hohe Porosität gestattet
beim sofort sich anschließenden Reduktionsprozeß ein ungehindertes Entweichen
der entstehenden Zinkdämpfe, während die Festigkeit des Koksgerüstes
verhindert, daß die Briketts beim Durchwandern der Retorte zerfallen und diese
verstopfen.
Nach der Verkokung hat das
Rohbrikett etwa 140 Gramm an Gewicht verloren: das Rohbrikett ist zum verkokten
Brikett geworden, unter weitgehender Erhaltung seiner Form. Schließlich ist es
durch den Verkokungs-Vorgang auf etwa 800°C vorgewärmt worden.
Jetzt ist es endlich so weit,
daß die letzte und hauptsächlichste Stufe der Verhüttung, die Reduktion zu
metallischem Zink, erfolgen kann.
Die Reduktion
Mit "Reduktion"
bezeichnet man die Umwandlung des im Röstgut enthaltenen Zinkoxyds in
metallisches Zink. Für diesen Zweck eignet sich in ausgezeichneter Weise die
Kohle. Sie "reduziert" das Zinkoxyd zu metallischem Zink, indem sie
diesem den Sauerstoff entreißt und selbst zu Kohlenoxyd verbrennt. Nehmen wir
wieder die chemische Formel zu Hilfe,
dann erhalten wir in vereinfachter Form:
ZnO + C = Zn + CO
Das Zink ist nunmehr frei von jeder chemischen
Bindung!
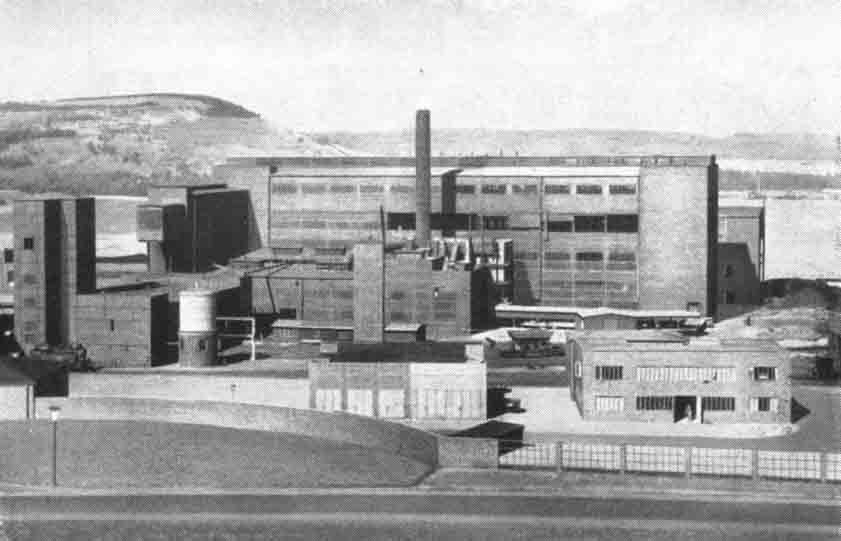
Zinkofen-Gebäude
Die glühenden Briketts, die
eben den Verkokungs-Prozeß durchlaufen haben, werden in großen Eisenkübeln
auf die Beschickungsbühne gehoben und in die Beschickungsöffnungen der
Zinköfen eingetragen.
Diese Zinköfen bestehen aus 8
Meter hohen geheizten Ofen- oder Brennkammern, die einen aus sehr gut
wärmeleitfähigen Steinen gemauerten Schacht, die Retorte, enthalten. Das
Steinmaterial besteht aus Siliziumcarbid (Carborundum). Unter völligem
Luftabschluß - die Retorte wird nur von außen beheizt - wandern die Briketts
unter ihrem eigenen Gewicht
durch den senkrecht stehenden Schacht kontinuierlich nach unten und werden im
beheizten Teil einer Temperatur von etwa 1300°C ausgesetzt. Dabei erfolgt durch
Einwirkung von Kohlenstoff und Kohlenoxyd die Reduktion des Zinkoxyds zu
metallischem Zink.
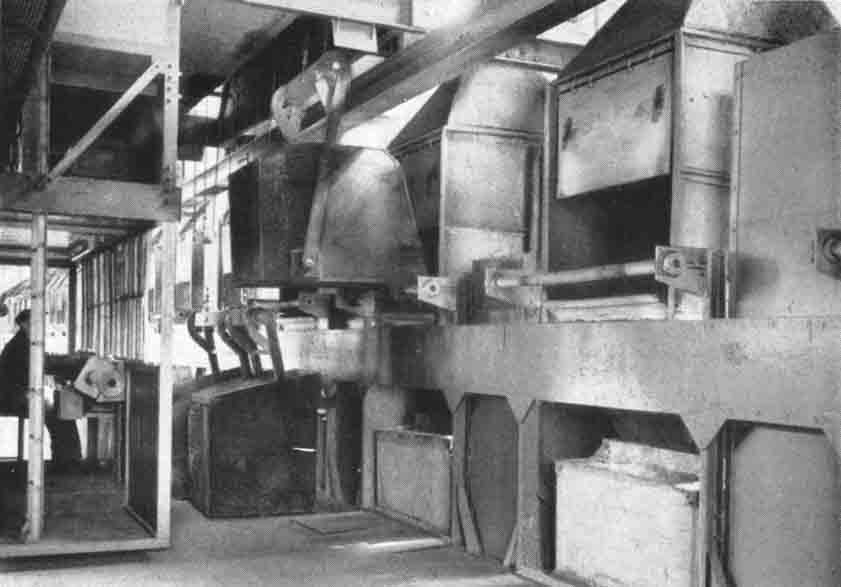
Auf der Beschickungsbühne
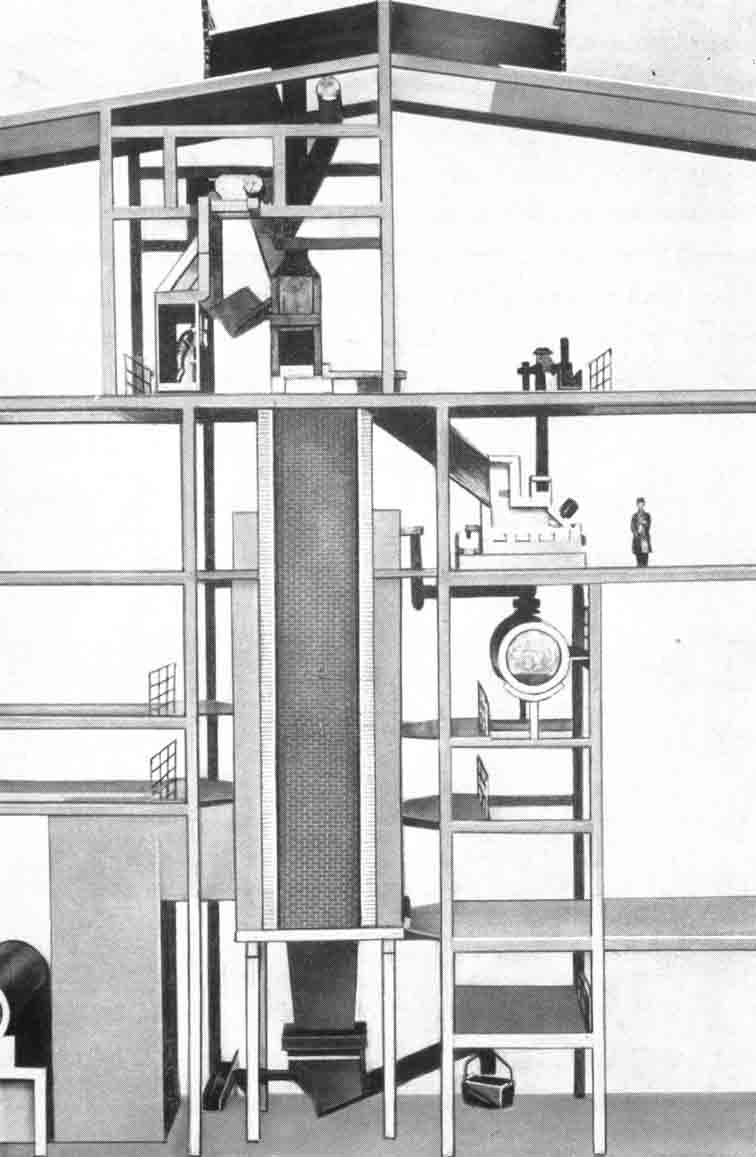
Modell einer Vertikal-Retorte
Da der Siedepunkt des Zinks
bei 907°C liegt, entwickelt sich zunächst ein zinkdampfhaltiges Gas, das am
Kopf der Retorte - kurz unterhalb der Beschickungsöffnung - zur Abkühlung in
einen sogenannten Sprühkondensator geleitet wird. Hier erfolgt die Kondensation
des Zinks, das nunmehr in flüssigem Zustand über einen Syphon kontinuierlich austritt
und durch eine beheizte Rinne in einen Sammelofen fließt. Von dort wird es als
Hüttenzink zu handelsfertigen Platten vergossen.
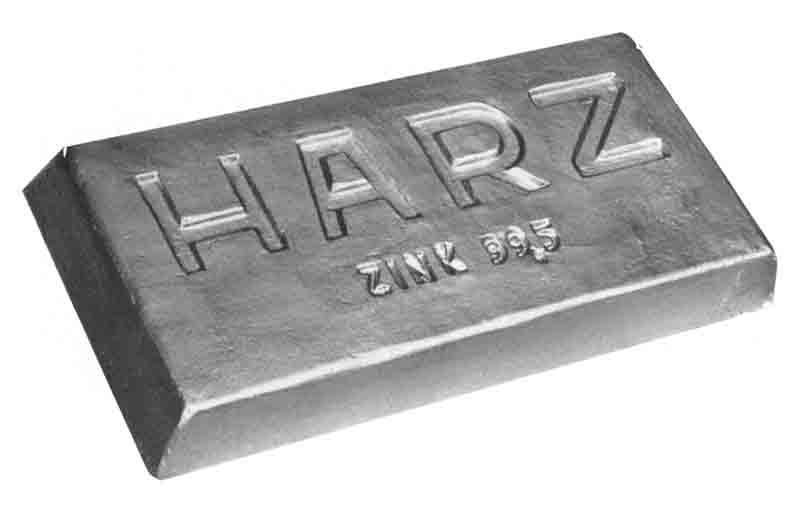
Hüttenzink "HARZ"
99,5
Am Fuß der Retorte werden die
entzinkten Briketts, die noch immer ihre ursprüngliche Form erkennen lassen,
als "Räumasche" ausgetragen. Sie enthalten nur noch wenig
Zinkanteile, fast alles im Röstgut enthalten gewesene Blei, Eisen und andere
geringe Mengen an Begleitmetallen.
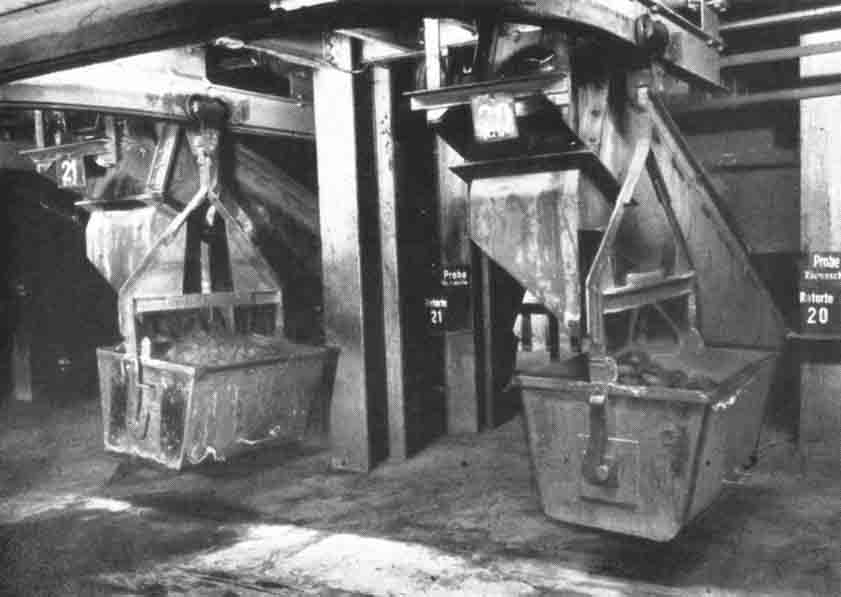
Austrag der Räumasche am Fuß
der Retorte
Damit ist die Verhüttung von Zinkerzen nach
einem einfach erscheinenden, aber doch umfangreichen Prozeß abgeschlossen.
Eigenschaften und Verwendung
von Zink 99,5 "HARZ"
Das in vorbeschriebenen Arbeitsgängen schon
mit großer Reinheit anfallende Hüttenzink gelangt unter der Bezeichnung "Zink
99,5 HARZ' in den Handel.
Die Durchschnitts-Analyse ist
folgende:
Zink |
99,50 % |
|
Kadmium |
0,010 % |
Blei |
0,33 % |
|
Kupfer |
0,004 % |
Eisen |
0,03 % |
|
Zinn |
0,002 % |
Die physikalischen und technologischen
Eigenschaften des Hüttenzinks sind:
Atomgewicht |
65,3 |
Spezifisches
Gew. fest |
7,14 |
Spezifisches
Gew. flüssig |
6,92 (bei
419°C) |
Schmelzpunkt |
419,5°C |
Siedepunkt
(760 mm QS) |
907°C |
Spez. Wärme
(0 - 300°C) |
0,094
cal/g·°C |
Schmelzwärme |
241
cal/g·°C |
Schwindung |
rund 1,5 % |
Elektr.
Leitfähigkeit |
16,9
m/Ohm·mm2 |
Elektrodenpotential
gegen Wasserstoff |
-0,76 V |
Zugfestigkeit
(gegossen) |
2,5 bis 4
kg/mm2 |
Dehnung |
0,3 bis 0,5
% |
Brinell-Härte
5/62,5/30 |
30 bis 35
kg/mm2 |
Das Hüttenzink wird vornehmlich von
Verzinkereien, Zinkwalzwerken, der Messingindustrie und der Farbindustrie
weiterverarbeitet.
Herstellung von Feinzink
"HARZ"
Für eine Reihe besonderer Anwendungsgebiete
genügt die Reinheit des Hüttenzinks nicht mehr. Es muß deshalb noch weiter
von den Begleitmetallen befreit werden. In der Hauptsache sind es Blei und
Kadmium, die durch ein Raffinations-Verfahren entfernt werden müssen.
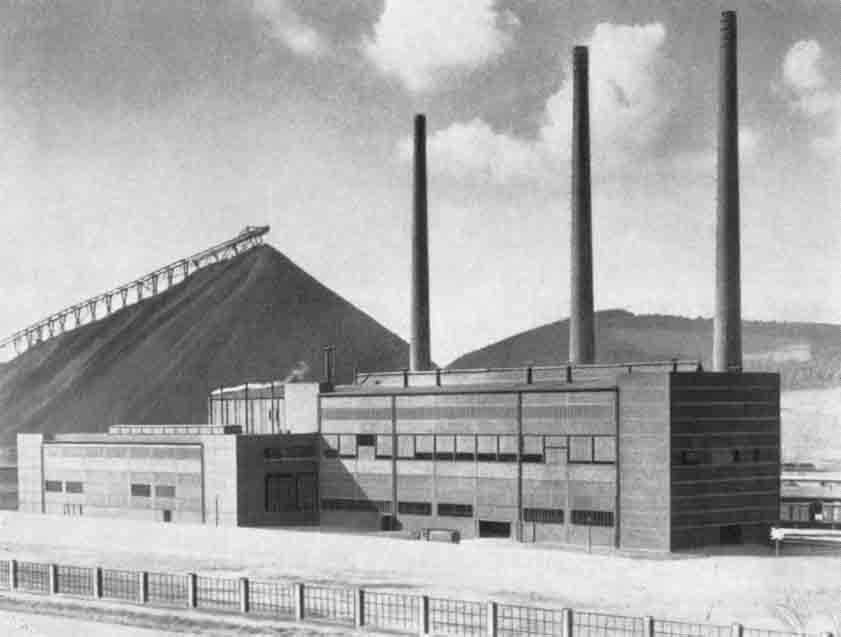
Feinzinkanlage und
Legierungsbetrieb
Die Zinkhütte Harlingerode
verfügt deshalb auch über eine Zinkraffinations-Anlage, die ebenfalls nach dem
New Jersey-Verfahren arbeitet. In dieser Anlage kann über die Hälfte der
Hüttenproduktion - je nach Bedarf - einer Verfeinerung unterzogen werden. Die
grundsätzliche Methode beruht auf der Abtrennung der Begleitmetalle auf Grund
ihrer vom Zink recht unterschiedlichen Siedepunkte.
Das Hüttenzink wird zur
weiteren Verfeinerung wieder eingeschmolzen und in Siliziumkarbid-Retorten von
kaskadenförmigem Aufbau erneut zur Verdampfung gebracht.
Eine solche Retorte besteht
aus etwa 50 rechteckigen Schüsseln, die aufeinandergesetzt sind und somit eine
"Säule" bilden. Die Verbindung zwischen den einzelnen Schüsseln zu
einem gemeinsamen Verdampfungsraum ist durch gegeneinander versetzte Öffnungen
in den Schüsselböden hergestellt. Die Säule steht mit ihrem unteren Teil in
einer Brennkammer. Oberhalb der Brennkammer, im nichtbeheizten Teil der Säule,
fließt das wieder eingeschmolzene Hüttenzink durch ein keramisches Rohr in den
Verdampfungsraum.
Die Temperatur wird so
geregelt, daß alle Zinkbegleitmetalle, deren Siedepunkt höher liegt als der
Siedepunkt des Zinks, flüssig bleiben, während das Zink (Siedepunkt 907°C)
und das Kadmium (Siedepunkt 767°C) überdestillieren. Über einem am Kopf der
Säule angeschlossenen kurzen Kanal tritt der Zinkdampf mit seinem geringen
Anteil an Kadmium in einen Kondensator. Hier kondensieren die Metalldämpfe
wieder zu flüssigem Metall, um über eine Rinne in eine zweite Säule zu
fließen.
Die erste Säule, die alle
schwerer flüchtigen Begleitmetalle insbesondere Blei (Siedepunkt 1740°C)
zurückhält, wird "Bleisäule" genannt. Am Fuß der Bleisäule
sammeln sich die Begleitmetalle in einem mit "Waschzink" bezeichneten
Zwischenprodukt an.
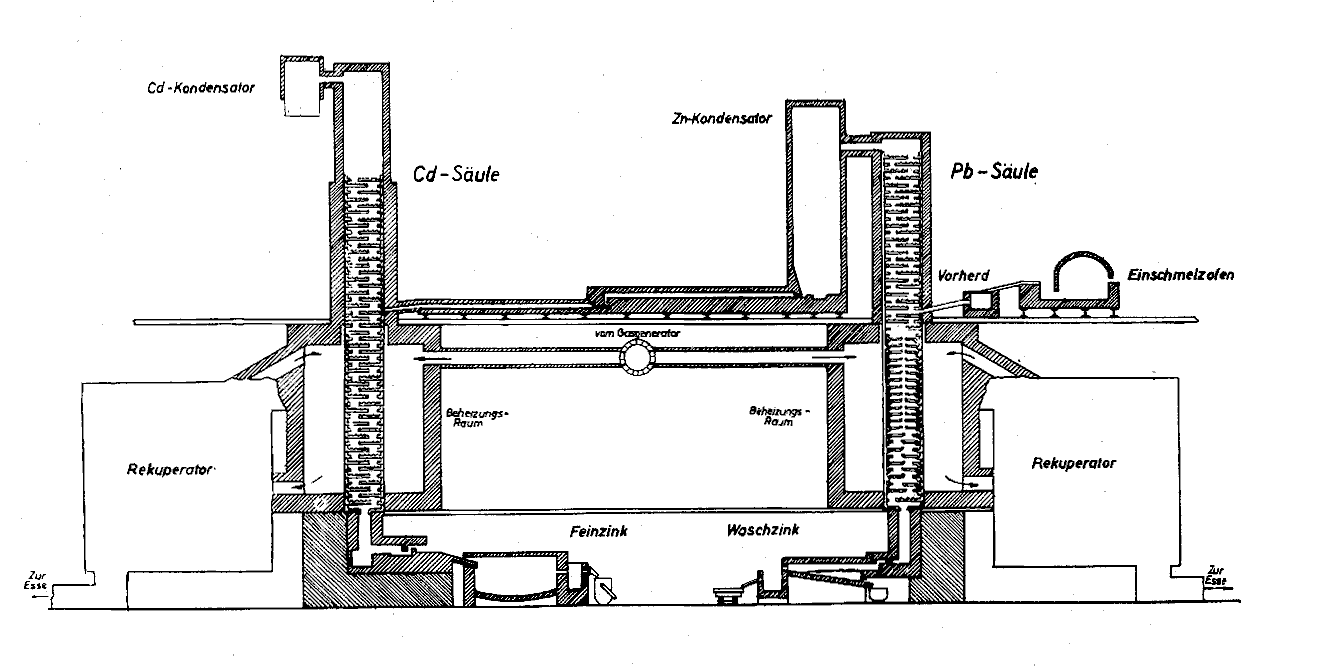
Schematischer Schnitt durch die
Feinzinkanlage mit nur einer Bleisäule
Die zweite Säule, die nur
noch zur Entfernung des Kadmiums dient, heißt demgegenüber
"Kadmiumsäule". Sie gleicht in ihrem Aufbau fast völlig der
Bleisäule. Die Temperaturen werden nunmehr so gehalten, daß zwar das Kadmium
verdampfen kann, nicht aber das Zink. Der zinkhaltige Kadmiumdampf tritt am Kopf
der Säule in einen Kondensationsraum über. Das vom Kadmium befreite Zink
durchfließt sämtliche Schüsseln und sammelt sich am Fuß der Säule, wo es
diese als fast chemisch reines Zink verläßt und aus einem Sammelofen in
handelsfertige Platten vergossen wird.
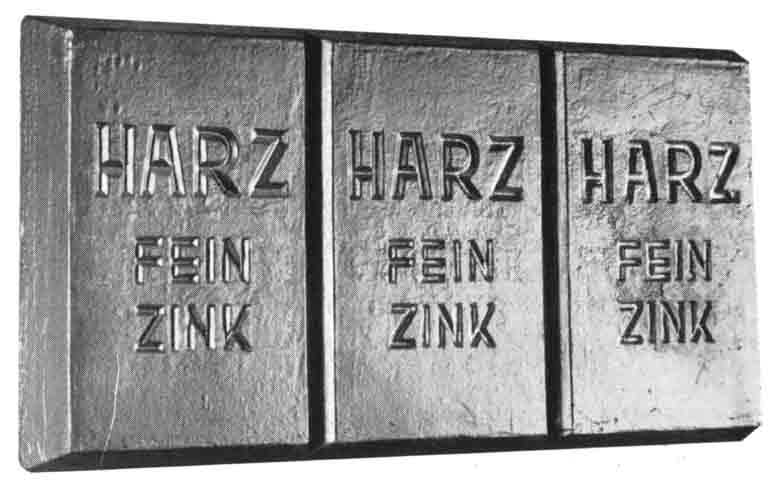
Feinzinkplatten
"HARZ"
Eigenschaften und Verwendung
des Feinzinks
Das Feinzink der Zinkhütte Harlingerode
gelangt unter der Bezeichnung "Feinzink HARZ" in den Handel. Die nur
noch sehr geringen metallischen Beimengungen liegen in der Größenordnung von:
|
15 g |
|
Blei |
je |
t |
Feinzink |
|
10 g |
|
Kadmium |
" |
" |
" |
unter |
2 g |
|
Eisen |
" |
" |
" |
" |
2 g |
|
Kupfer |
" |
" |
" |
" |
1 g |
|
Zinn |
" |
" |
" |
Die physikalischen und
technologischen Eigenschaften des Feinzinks weichen von denen des Hüttenzinks
nur ganz unwesentlich ab, so daß für den allgemeinen Gebrauch ohne weiteres
die zuvor genannten Werte herangezogen werden können.
Das Feinzink wird für den
wichtigen Sektor der Feinzinklegierungen, für die Fertigung von besonderen
Walzerzeugnissen, für die Durchführung von Spezialverzinkungen und für die
Herstellung hochwertiger Messinge benötigt. Neuerdings findet es mit Erfolg
auch für das "kathodische Schutzverfahren" zur Verhinderung der
Korrosion an Eisenteilen, besonders bei in der Erde verlegten Rohren (Pipelines)
und Schiffskörpern Verwendung. Ein weiteres Anwendungsgebiet liegt in der
Verwendung als Zinkstaub für besonders aufgebaute Rostschutzfarben und das
Zinkspritzen zur Schaffung korrosionsbeständiger Überzüge
Feinzinklegierungen
Die Zinkhütte Harlingerode
verfügt über eine Legierungsanlage, die erst nach dem Kriege unter
neuzeitlichen Gesichtspunkten erstellt wurde.
Das Feinzink, welches mit der
vorauf beschriebenen großen Reinheit die Raffinationsanlage verläßt, wird
unmittelbar in flüssigem Zustand den Legierungsöfen zugeführt, wodurch das
nachteilige Wiedereinschmelzen fester Feinzinkplatten erübrigt wird.
Die bis zu 17t fassenden
Legierungsöfen sind gasbeheizt und mit einer Rührwerkeinrichtung versehen. Die
Legierungszusätze, vornehmlich Aluminium und Kupfer, werden in besonderen
Tiegelöfen eingeschmolzen und danach unter Einhaltung besonderer
Temperatur-Bedingungen und Beachtung einer guten Durchmischung des Bades in der
jeweils benötigten Dosierung dem Zink zugesetzt.
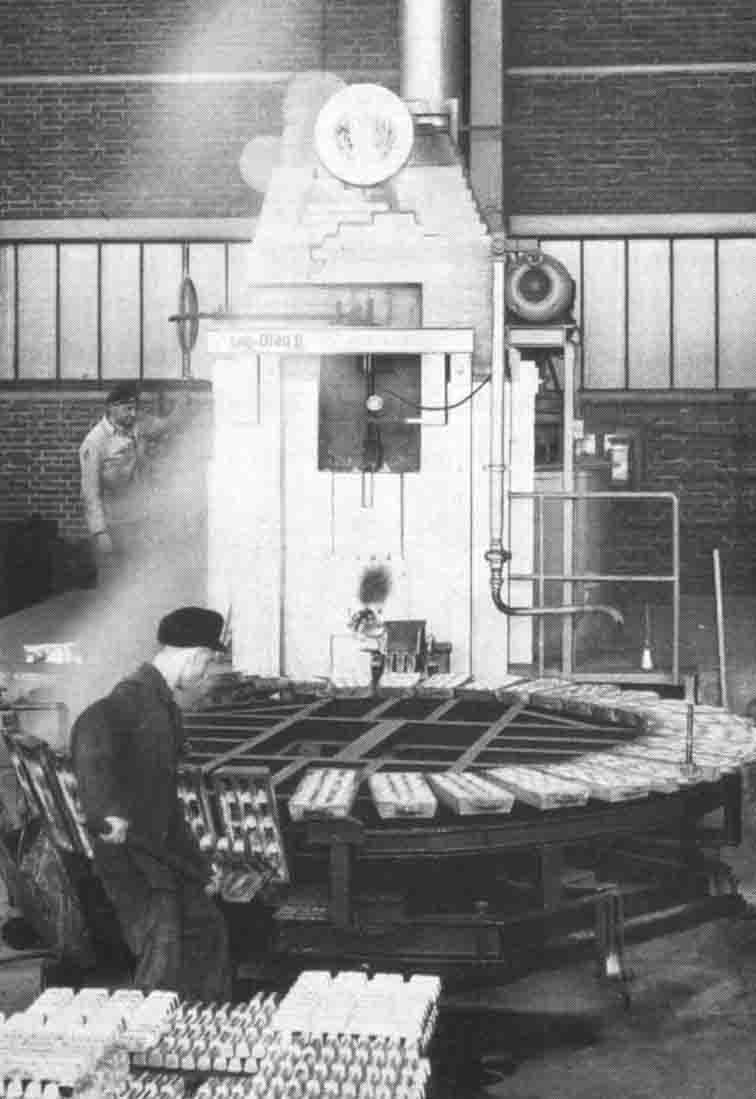
Legierungsofen mit
Gießkarussel
Je nach Anforderung der Abnehmer werden
Masseln, Walzplatte oder Rundbolzen hergestellt.
Es sei an dieser Stelle auf das Heft
"Feinzinklegierungen HARZ" verwiesen, in welchem alle heute gängigen
Feinzinklegierungen mit ihren technologischen
Eigenschaften und Verarbeitungsbedingungen beschrieben sind.
Die Anwendungsgebiete für
Feinzinklegierungen sind nach dem Vorbild des Auslandes in stetiger Ausweitung
befindlich.
An erster Stelle sieht heute
der Druckguß mit einer Vielzahl von Fertigungsteilen für die verschiedensten
Industrien und Bedarfsartikel. Es sei hier nur an Kraftfahrzeugteile,
Büromaschinen, Haushaltsgegenstände, Möbelbeschläge, Musik- und Spielautomaten, optische Apparate, elektrotechnisches Zubehör, Spielwaren,
Reklameartikel und vieles andere mehr erinnert.
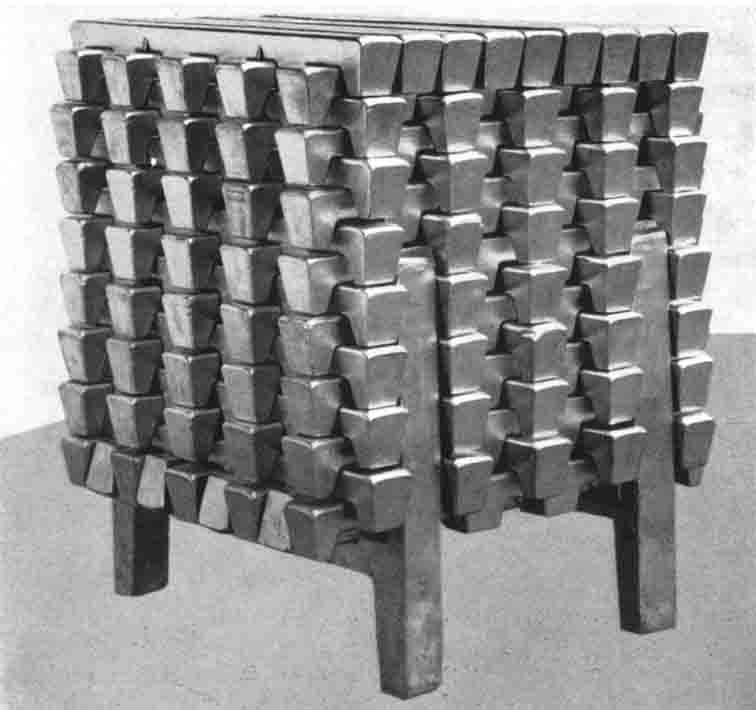
Legierungsstapel
|